The magnetic chip conveyor is a vital tool in industries dealing with metalworking or machining, as these processes often generate large quantities of shavings and waste. The efficient removal and handling of metal chips is crucial in industries such as automotive manufacturing, aerospace and machining. Traditional conveyor systems may struggle to manage these sharp, small, and often tangled metal parts. These challenges are solved by magnetic chip conveyors, which use powerful magnets that attract ferrous metals and transport them safely. This creates a safer and cleaner working environment. By automating chip removal, these conveyors reduce material losses, eliminate manual handling and increase overall efficiency. They are indispensable for many industrial applications.
Magnetic chip conveyors are designed with powerful magnets embedded within or beneath the conveyor belt. The magnets produce a magnetic field which attracts ferrous material, like metal chips and holds them in place as they move along the conveyor. This ensures that metal shavings, even small ones, stay in place as they are transported from the machine or work area to a designated collection point. The use of magnetic force to move the chips prevents them from falling off the conveyor, thus reducing material loss and maintaining the flow of production. Traditional conveyor systems, on the other hand, often rely on friction to move materials, which can lead to slippage, misalignment, or clogging. Magnetic conveyors eliminate these risks by providing a more secure and stable means of transporting metal debris, making them especially useful in environments where metal chips are generated continuously.
The versatility of magnetic chip conveyors is also well-known. These systems can be customized to meet the specific needs of different industries and applications. Whether the conveyor system needs to transport materials horizontally, vertically, or at an incline, magnetic conveyors can be designed to fit the layout of the production facility. The conveyors can be designed to accommodate a variety of chip sizes, ranging from tiny metal filings up to large, heavy metal shavings. The magnetic field strength can be changed depending on the weight and size of the material being moved. This adaptability allows businesses to optimize their conveyor systems for the specific demands of their production lines, whether they are dealing with heavy-duty scrap metal or fine metal particles. The ability to customize the system ensures that magnetic chip conveyors can be used in a wide range of metalworking environments, from small workshops to large industrial plants.
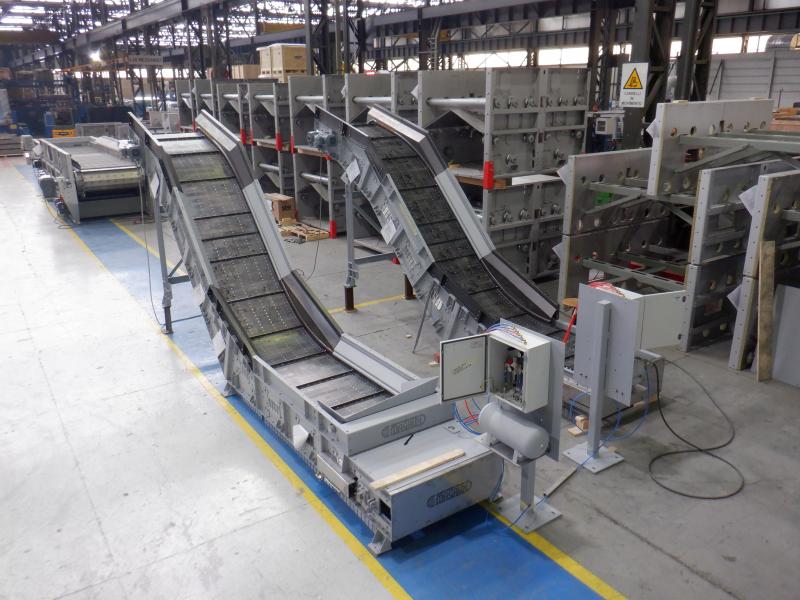
Magnetic chip conveyors can improve operational efficiency while reducing downtime. Traditional Magnetic Chip Conveyors rely on friction to move materials, which can cause wear and tear on belts and components over time, leading to increased maintenance costs and frequent repairs. Magnetic conveyors, by contrast, operate with minimal friction because they use magnetic force to secure the chips to the belt. This reduction in friction results in less wear on the system, which means the equipment lasts longer and requires less maintenance. Magnetic conveyors also help to streamline the production process by eliminating manual handling of chips and minimising material contamination or loss. Material flow is continuous and efficient, ensuring that the production line remains operational and uninterrupted. To acquire supplementary information kindly check out www.tecnimetal.com/project/trasportatori-magnetici/
Magnetic chip conveyors are also low maintenance. The friction caused by the material being moved and the conveyor belt can cause traditional systems to require frequent maintenance. Over time, this friction causes the conveyor belt to degrade, and parts such as rollers and gears can become damaged, leading to expensive repairs and replacement costs. In contrast, magnetic chip conveyors experience less wear because they employ magnets to transport and secure materials. This reduces friction. As a result, magnetic chip conveyors typically last longer and require less frequent maintenance, saving businesses both time and money. Their simplicity also makes maintenance easier as there are fewer components that need to be serviced or inspected. Magnetic chip conveyors are a cost-effective and reliable solution for industries that need to minimize downtime.
Magnetic chip conveyors also contribute to waste reduction and sustainability. In industries such as metalworking and machining, recycling metal chips can provide significant cost savings, as well as environmental benefits. Magnetic chip conveyors efficiently transport the collected metal debris to recycling stations, where it can be sorted, processed, and reused. These conveyors reduce costs by facilitating recycling and collection of metal waste. They also support environmentally friendly practices. Recycling metal chips also conserves valuable resources by ensuring that scrap metal is reused rather than discarded. Magnetic chip conveyors are a great way to help businesses reach their sustainability goals. They support the recycling and reusing of materials which reduces the impact of metalworking.